High throughput rates, long service-lives and effective cutting performance in continuous operation make maximum demands on the materials used for rotary shears in waste incineration plants. Such twin-shaft shredders are used, for example, to prepare domestic and commercial waste prior to thermal valorisation as a secondary fuel. Their cutting tools, exposed to the most adverse conditions, consist of cutter disks with barbed shredder teeth.
Harden Machinery Ltd., China’s largest manufacturer of size reduction machinery for industrial and municipal waste, has equipped the rotary shear of a large municipal waste incineration plant with this high-performance steel. The plant’s cutter disks were produced from Dillidur 550 by BMM, the steel stockholding partner for Dillidur plate in China. Wear measurements performed at regular intervals during operation indicated a service-life longer by up to 30 percent for the Dillidur 550 cutters compared to the Dillidur 500 wear-resistant steel previously used.
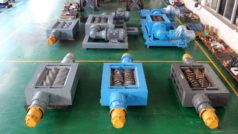
Twin-shaft shredders are used to prepare domestic and
commerical waste prior to thermal valorisation as a secondary fuel. (Foto: Dillinger)
Dillinger’s highly wear-resistant Dillidur special steel has proven its capabilities around the world wherever critical components are subjected to extreme abrasive wear. Dillidur, thanks to its special microstructure and hardness, assures up to five-fold greater wear resistance than conventional steels. The steels owes this extreme wear-resistance, with hardnesses ranging from 325 to 550 Brinell, to the sophisticated alloying concepts and special processes used for its production. After rolling, an accelerated and uniform cooling process in the hardening quench imparts to the steel its hard, fine-grained structural state with a homogeneous hardness distribution of the plate. According to the company Dillidur combines the special resistance to wear thus achieved with good working properties for welding and forming, and low preheat temperatures. With thicknesses of up to 52 millimetres – and an expansion of the portfolio to 100 millimetres planned – plus a hardness of 550 Brinell, Dillidur 550 meets customers’ wishes for significant increases in service-lives achieved via plates of maximum thickness, weight and wearresistance.
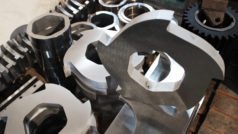
The cutting tools, exposed to the most adverse conditions, consist of cutter disks with barbed shredder teeth. (Foto: Dillinger)
Continuous service in waste incineration plant
According to Dillinger BMM was one of the first users to gain experience with Dillidur 550. BMM, with registered offices in Shanghai and two further branches in China, has specialised in the sale and use of these wear-resistant steels since its founding in the year 2000. In addition to the various Dillidur grades, the BMM range also includes the high-strength quenched and tempered fine-grained structural steels of the Dillimax series. The company’s leading know-how in the use of Dillidur, acquired in the course of nearly twenty years of experience, makes BMM a highly popular partner for challenging tasks. China’s leading manufacturer of shredder systems, Harden Machinery, based in Zhongshan, Guangdong, has thus for years now put its faith in Dillidur steels and BMM’s proven high production capabilities. For a high-capacity plant for pre-comminution of domestic waste at a waste incineration plant, Harden Machinery commissioned BMM to fabricate a new set of cutters for the twin-shaft shredding mechanism of the rotary shear. The facility operates 16/7 throughout the year, with a daily throughput rate of 500 to 800 tonnes per unit. Continuous comminution reduces the volume of the flow of waste, in order subsequently to permit the extraction of the constituents not suitable for thermal valorisation.
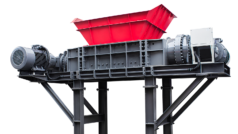
Harden Machinery commissioned BMM to fabricate a new set of cutters for a high-capacity plant for pre-comminution of domestic waste at a waste incineration plant. (Foto: Dillinger)
Trouble-free operation of the rotary shear is thus the top priority to assure uninterrupted operation of the waste incineration plant, and downtimes caused by cutter fracture or wear are correspondingly feared. Harden Machinery has therefore put its trust in Dillidur 500 for many years when selecting the material for the cutters. The cutter disks produced from this material have exhibited service-lives up to now of two to four years, depending on the composition of the feed material. Each of the up to three-metre-long shafts of the twin-shaft shredding mechanism features up to thirty of these cutter disks. These disks, each 50 millimetre thick and 600 millimetre in diameter, contrarotate on the shafts, drawing with their barbed shredder teeth the feed material into the cutting gap, where it is comminuted. The even harder wear-resistant Dillidur 550 steel was used for the first time for the new set of cutters at the suggestion of James Meng, founder-owner of BMM.
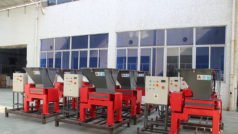
The facility in Zhongshan operates throughout the year,
with a daily throughput rate of 500 to 800 tonnes per unit. (Foto: Dillinger)
“It goes without saying that a higher-alloyed material has to be worked differently to other steels”, James Meng states. For this reason, tests were firstly performed at his company, in order to gain experience with the new grade. He was able here to count on support from Dillingen. He was provided not only with material samples, but also technical documentation and personal support on specific questions. One example here is preheat and insulation of plates for cutting: they are maintained after cutting at the elevated temperature for at least 24 hours by using heat insulation. BMM now uses this specific experience and the documentation from Dillingen to organise seminars for customers wishing to use this material themselves.
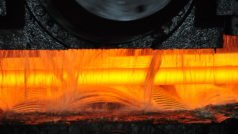
Dillidur steels are homogenized down to the core by rolling with 11,000 tons of rolling force. (Foto: Dillinger)
Service-lives longer by 30 percent
According to Dillinger this far-reaching know-how proved its worth once again during the production of the cutters for Harden Machinery’s rotary shear. In a first operation, the cutter disks were cut from the plate by means of plasma cutting, in order to minimise internal stresses caused by the input of heat into the material, and thus the danger of cracking. BMM selected the wire-cut EDM process for the detailed cuts. This method permits extremely precise cuts without the generation of internal stresses. BMM’s priority during subsequent CNC milling and polishing machining was adherence to tolerances of 10 µm – in processing terms, no problem for this experienced component manufacturer, even with Dillidur 550.
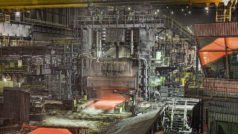
With thickness of up to 52 millimetres plus a hardness of 550 Brinell, Dillidur 550 increases service-lives significantly. (Foto: Dillinger)
“Machining time input with this new steel was around five percent higher, and tool wear around a third higher, compared to production of the cutters from Dillidur 500”, James Meng continues. In his estimation, these extra costs are not in any way significant, in view of the in any case overall high production costs. The new set of cutter disks has now been in use in the rotary shear of the waste incineration plant for 12 months. The plant operator measures wear at regular intervals, in order to be able to estimate the remaining service-life of the cutters. They have more than met his expectations from this highly wear-resistant steel already: cutters fabricated from Dillidur 550 convince their users with a significantly greater resistance to wear compared to the service-lives of the Dillidur 500 materials previously used.
The data measured indicates a service-life longer by 25 to 30 percent for the cutter disks consisting of the even harder material, the company says. And James Meng is also correspondingly pleased with this new high-performance steel from Dillinger: “It’s only in the nature of things that this more highly alloyed material is much harder and therefore somewhat more difficult to work”. He sees no problems in working this steel, however, using modified tools, in some cases, and a modified cutting speed. For James Meng, too, the benefits are immediately apparent: “Thanks to its greater hardness, Dillidur 550 assures significantly higher service-lives for components exposed to extreme stresses, and thus even greater customer-satisfaction”.