Some sorting applications are far more complex than others and cannot be handled using conventional methods – for example sorting silicone cartridges. Since they comprise a polyethylene (PE) outer wall, they are valuable materials for recycling. Silicone residues inside the cartridge can, however, contaminate pure PE products, even rendering them unusable, and meaning that they have to be removed from the material flow.
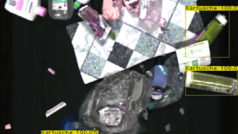
The first application of AI-supported object detection Intelligent Object Identifier is specialized in the detection of silicone cartridges to achieve silicone-residue-free PE products. Photo: Steinert
The Intelligent Object Identifier has been developed for the sorting of silicone cartridges; an Artificial Intelligence (AI)-supported object detection system for sorting machines that detects and isolates these cartridges using optically detectable characteristics.
In the future, this technology will also support other sorting tasks or indeed make them possible for the first time. For example, Steinert is working on an addition to the sorting program to separate polyethylene terephthalate (PET) bottles and trays that will further improve sorting reliability thanks to a new object detection feature.
What makes the Steinert solution so special is the fact that it can be integrated without any additional sensorics and is downward compatible with Unisort machines dating back to 2018 with a combination of near-infrared (NIR) and colour cameras.
According to Steinert, the Unisort PR EVO 5.0 features a design which is much easier to maintain and delivers advanced sorting results. Dynamic calibration monitors the spectrum of the belt lighting, which is changing all the time in response to external factors, and does so without interrupting the sorting process. Revamped light boxes ensure improved detection in the long term while also simplifying maintenance. Coupled with software updates that are being developed all the time, optimised valve blocks then guarantee a consistently precise separation of the waste flow. An optional automatic white balance reduces the intensity of maintenance, eliminating further manual stages, thereby improving staff management and making new levels of flexibility possible.