By designing Austropressen presses each for a specific purpose, the company places a focus on sustainability, environmental awareness and energy efficiency. Austropressen, with its high-performance press systems and energy efficiency, is a valuable partner of the international waste and recycling industry.
Current customer projects with customised solutions such as for Vöslauer Mineralwasser GmbH, Austria, and Retour Matras BV, the Netherlands, clearly demonstrate Austropressen’s successful implementation of recycling and reuse.
Into the future with rePET
With its market share of over 40%, Lower Austria’s Vöslauer Mineralwasser GmbH ranks top of the Austrian mineral water market. In addition to bottling and distributing own brands such as Vöslauer Mineralwasser or Vöslauer Flavours, the company also produces the brands Almdudler, Pepsi Cola and 7up under license.
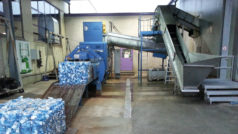
Photo: Roither Maschinenbau
The challenge: In 2018 Vöslauer became the first Austrian company to develop marketable 100% rePET (recycled PET) bottles. Vöslauer aims by 2025 to produce all PET bottles from 100% rePET. Another paramount requirement is efficient and CO2-saving transport to their recycling partners. To achieve this, all PET bottles are pressed into bales, with energy- and resource-conservation a top priority here. The result is obvious: high bale weights ensure fully utilised transport capacities. Long plant service life is also very important for Vöslauer.
The solution: The fully automatic Austropressen APK-D55 channel baling press was selected as the answer to Vöslauer requirements. A specially designed in-feed system with perforator was added for reliable supply of the plant.
PET bales weighing 300 kg are produced with 550 kN pressure force and for a calculated 135 m³/h throughput. A perforator will fully empty bottles containing any residual fluids. This will guarantee stable and heavy bales. To ensure resistance to any aggressive residual fluids (sugar from lemonade), the conveyor system is manufactured using entirely stainless steel (Niro). The channel baling press is furthermore protected with a special epoxy resin coating. Exchangeable HARDOX base plates ensure low wear and increased service life.
A 22 kW drive with sensor-controlled switch-off should material infeed fail will guarantee efficient use of energy. Specially developed hydraulic units and an oil care system (cooling, heating, cleaning all in one) ensure energy-efficient operation and serve to extend the service life of hydraulic equipment and fluid. A patented cutting system will minimise jamming of material, energy consumption and wear of cutting tools. The fully automatic Austropressen DRILLFIX 4-fold bale binding system will ensure trouble-free and wire-saving operation. Reliable and trouble-free binding is assured by a wire insertion system. The channel baler communicates with the internal network to automatically log machine data (number of bales, operating hours, error messages).
Foam material presses for efficient mattress recycling
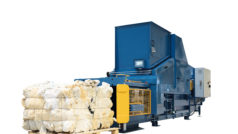
Photo: Roither Maschinenbau
The retail sector regards Retour Matras as the Dutch mattress recycling specialist. The company collects, shreds, separates and transports the individual materials. The materials are sorted by foam, latex and textile cover, compressed into transportable bales in presses and sold to recycling companies for reprocessing.
The challenge: Retour Matras BV requires baling presses to optimally prepare and bundle the different materials for transportation. In terms of conveyance, filling and binding the bales, high throughput, trouble-free operation and maximum automation are essential requirements.
The solution: Retour Matras are using two types of Austropressen models for material compaction: the semi-automatic AP-42F and the fully automatic APK-F60. Both are designed to handle foam and expanding materials and offer high throughput rates, high bale weights, speed and continuity to meet all company requirements. Both Austropressen models feature a user-friendly display showing:
– Flow chart (of pressing process)
– Information and technical data for operators (fill level, oil temperature etc.)
– Error messages with notes for remedy, tips etc.
The AP42F-1400 with automatic filling and compaction in the direction of pressing, has a 22 kW drive for 420 kN pressure force. The large filling hopper allows for high throughput and large bale sizes (1000 x 700 x 1300 mm) and bale weights of approx. 400 kg (depending on material). Message on the display indicates that bales are ready for manual binding. The binding process with simple Quick-Link wire systems for speed: 8-fold in cross binding (3 x horizontal and 5 x vertical). Finished bales with ideal dimensions for container transport are automatically ejected.
The fully automatic APK-F60 features a 22 kW drive for 600 kN pressure force, producing 1100 x 750 x 1200 mm bale sizes. The reinforced system with retaining claws ensures free filling space and reliable PLC control guarantees trouble-free continuous operation. The Austropressen Drillfix automatic wire tying system will use 9-fold cross binding (4 x horizontal and 5 x vertical) to perfectly wrap each bale. Depending on material, bale weights up to 450 kg will be achieved. High stability and optimal bale shape will allow up to three bales of stacking height. This guarantees maximum utilisation of truck and container transport capacities.