LIB performance is especially dependent on the active cathode material, which commercially consists of certain type of electrochemically active compound types containing Co, Ni, Mn and Fe in different proportions, in addition to Li. A significant number of researchers have tried to develop processes to repair or recycle cathode materials in spent LIBs.
In general, there are four types of recycling technologies including, mechanical treatment, hydrometallurgical treatment, combination of thermal pre-treatment and hydrometallurgical methods, and finally pyrometallurgical treatment. XProEM Ltd has developed a proprietary technology called solid state subtractive metallurgy (S3M) and it has already shown great potential as a disruptor to existing hydro and pyro chemical processes. S3M can directly convert waste cathode material (“Black Mass”) into separable forms of chemicals containing Li, Ni and Co in solid state.
However, in todays LIB recycling scenario, spent battery handlers or used EV handlers are interested in turnkey solutions and recycling companies are expected to have a steady feed of Black Mass for their recycling operation. In light of this, XProEM Ltd. developed its own proprietary variable vacuum vapour extraction (V3E) process which complements its S3M process to provide turnkey solutions to spent battery and used EV handlers.
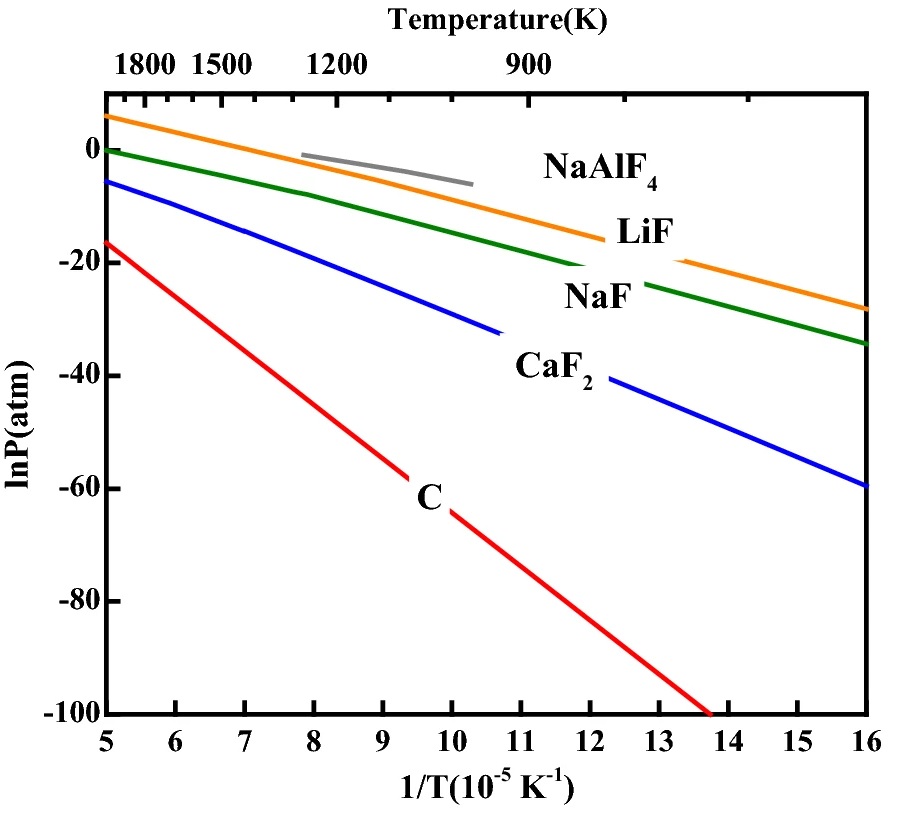
Fluorides have different vapour pressures over a wide range of temperature. Source: XProEM Ltd
The V3E process can accept spent battery packs and physically separate it robustly and safely into Black Mass which becomes a feed to the S3M process, among many other recycled components. V3E includes the physical separation of spent LIBs to recover the valuable components by using vacuum treatment to extract and recover volatile matters such as electrode binder, electrolyte solvent and salt. It is then followed by shearing and crushing steps which disintegrate the electrolyte-depleted battery pack. The subsequent comminution can further reduce the size of shredded particles of enclosed components such as casing, current collectors, separator and other materials, which are separated using a series of physical separation techniques thereafter.
Vacuum extraction principle
Vacuum extraction is an extraction technique performed at low and ultra low pressures, which allows the purification of mixtures or compounds not readily separable at 1 atm pressure or simply to enhance the separation rates at reduced energy consumption. Vacuum extraction separates compounds based on differences in boiling points and vapour pressures. This technique is used when the boiling point of the desired compound is difficult to achieve or will cause the compound to dissociate. A low pressure decreases the boiling point of compounds. The reduction in boiling point can be calculated using a temperature-pressure relationship based on the thermodynamic principle provide by the Clausius–Clapeyron equation.
Vacuum separation is very popular in food, petro chemical and water purification industries and XProEM Ltd has customized the vacuum extraction reactor and the operating conditions to implement it in the physical separation process of treating used LIBs. LIBs contain compounds with different evaporation behaviour which includes binders, electrolytes, and a wide variety of fluorides. Each of these compounds have different boiling points and vapour pressures, and hence the ability to apply variable vacuum is highly critical. Figure 1 below shows how different fluorides have different vapour pressures over a wide range of temperature.
Variable Vacuum Vapour Extraction
The V3E process includes a method for physically disintegrating spent lithium ion batteries and recovering essentially all valuable materials in reasonably high purity. Vacuum extraction and distillation are applied to separate and recover volatile matter such as electrode binder, electrolyte solvent and salt. Crushing and comminution are subsequently applied to tear and disintegrate the electrolyte solvent from the depleted battery pack, and reduce the size of shredded particles of enclosed components such as the steel and aluminum casing, copper and aluminum foils, membrane separator and other bulky materials, for subsequent separation and recovery.
The electrode materials, namely lithium bearing metal oxides and graphite, are recovered in their native powder state through a series of physical separation techniques including sieving and gravity separation. A mixture of Argon and Carbon dioxide (“CO2”) is applied as an inert gas to avoid fires from LIB pack discharging and to facilitate vacuum extraction as a heat source and shrouding gas. The spent lithium ion battery pack is firstly discharged in a saline solution to release any residual electrical powder. The fully discharged LIB pack is then opened to allow electrolyte to be drained first by gravity.
After sufficient draining takes place, the drained LIB pack is heated to a low temperature range, to drive out any residual electrolyte solvent trapped inside the electrode or membrane separator, in an enclosed chamber with partial vacuum conditions and an inert atmosphere. Differential heat treatments and vacuum strength can be applied depending on whether HF is present in the system, as indication of reactions involving phosphorus pentafluoride (“PF5“) and water or organic solvents having taken place.
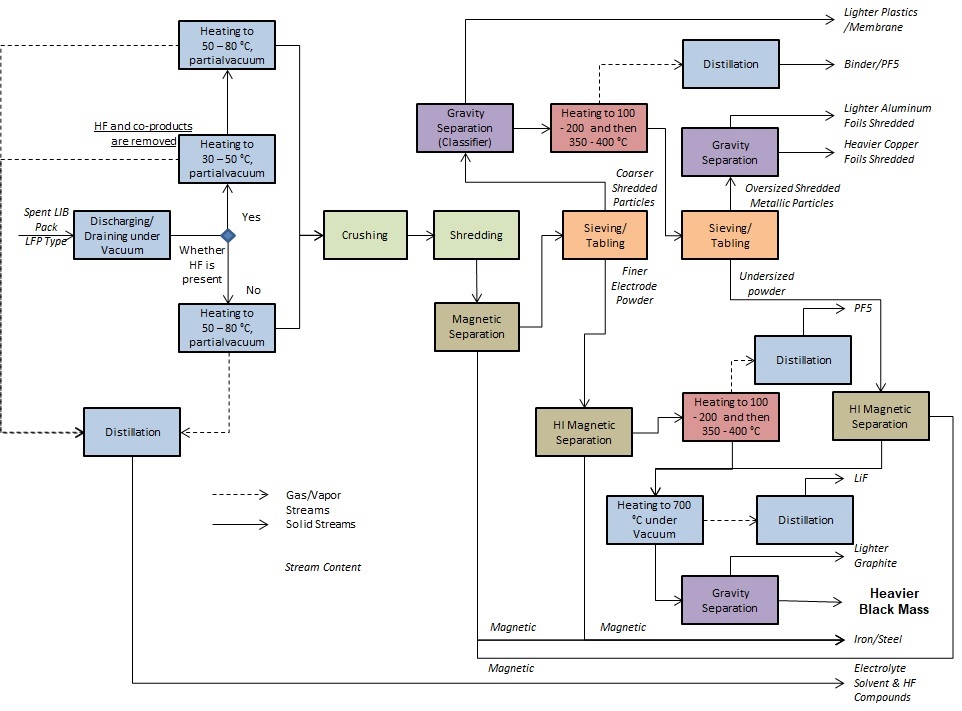
Flowsheet for the V3E process for LFP type batteries Source: XProEM Ltd
After HF and other co-products from PF5 reaction are thoroughly removed, the vacuum chamber can resume its regular configuration and continue to evaporate the electrolyte solvent, which is recovered via condensation afterwards. Once the electrolyte solvents and other volatile substances are extracted out of the LIB pack, the LIB pack is crushed using a commercial crusher to disintegrate the components into smaller pieces.
To fully liberate some of the materials and reduce the overall sizing of the mass flow, crushed LIB pack pieces are shredded using additional grinding equipment. The finer particles are then sent for dry magnetic separation where majority of magnetic active steel casing debris is removed and the rest of the materials are applied through sieving where finer powders, mostly liberated cathode and anode, are separated from coarser shredded particles. The coarser particles are subsequently sent through dry gravity separation to remove lighter debris of plastic, aluminum-plastic, and membrane from heavier metallic particles.
To further liberate the cathode powders, which are tightly glued to the metallic current collector, the heavier metallic particles are heated to an intermediate temperature to remove the organic binder material through evaporation and decomposition. For the electrolyte salt, lithium hexafluorophosphate (“LiPF6”) carried over with electrode powder, it will also undergo thermal decomposition under heating and dissociate into volatile PF5 and lithium fluoride (“LiF”) powder, and PF5 will exit the system in the vapor phase along with effluent from the decomposition of the binder material.
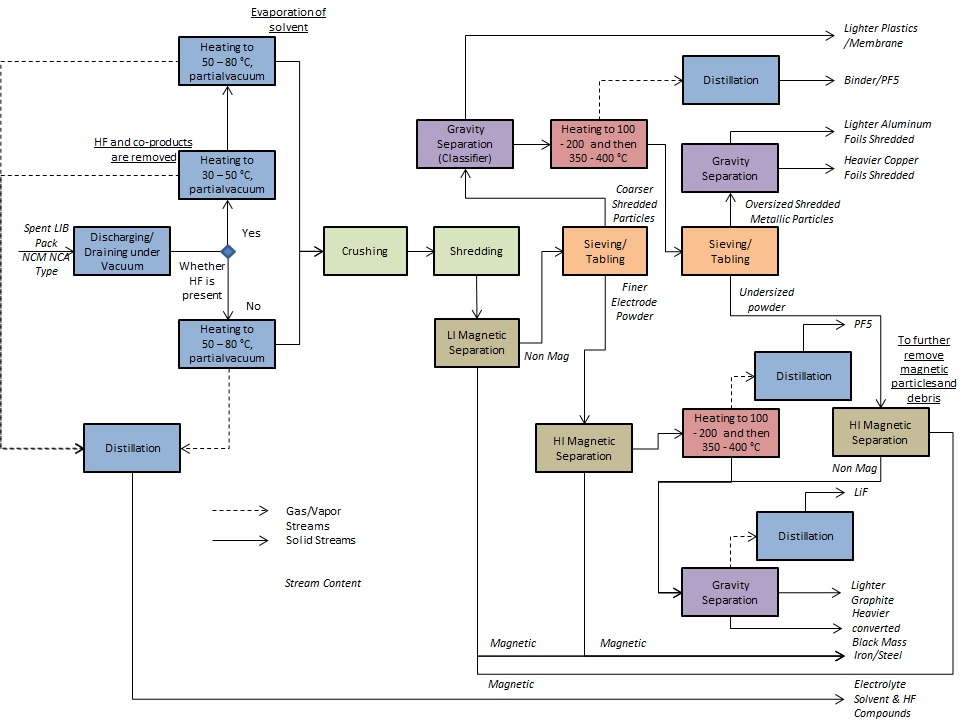
Flowsheet for the V3E process for NCM/NCA type batteries. Source: XProEM Ltd
After the extraction of the fluoride-bearing vapor, the remaining coarser material is sent to undergo another pass of sieving to separate finer electrode powders recently liberated from the shredded metallic foils. The oversized shredded metallic pieces are then applied through another pass of gravity separation to separate heavier copper foils from the lighter aluminum foils. The finer powders need to undergo high intensity magnetic separation to remove any remaining iron-bearing particles and debris. Subsequently the non-magnetic powder is heated up to with moderate heating to fully decompose any remaining LiPF6 and evaporate away any PF5 generated. The LiF generated concurrently with PF5 will join the LiF already present in the powder.
The last step is to separate LiF from the cathode and anode powder. For the less thermally stable cathode active material such as lithium nickel cobalt manganese oxide or lithium nickel cobalt aluminum oxide, calcination under the presence of graphite at an intermediate temperature is applied to convert the cathode into a preferred transition metal oxide state, in order to increase the overall density of the cathode powder. Subsequent steps involve gravity separation of the denser cathode from the much lighter LiF and graphite. For more thermally stable cathode active material such as lithium iron phosphate, vacuum extraction can be applied to remove relatively volatile LiF from the mixture and the fluoride-free powder can be sent for the last step of gravity separation to isolate graphite from the denser cathode material of lithium iron phosphate.
Conclusions
XProEM Ltd has successfully designed the V3E process to produce Black Mass from all types of used EV LIBs and is a perfect complement to its piloted S3M process. Also, the versatile V3E process separates more by-product streams to boost revenue. The combination of V3E-S3M package certainly offers a complete solution to provide turnkey solutions to used EV handlers and spent battery handlers; and also ensures long term Black Mass availability to feed the S3M chemical separation and the right chemistry of Black Mass needed for operating S3M process. In addition, V3E design offers flexibility in its configuration to allow highly compatible tie-ins with many chemical separation processes and different feed materials.
www.xproem.com