“Companies that can provide solutions for the transformation to a circular economy will have a crucial competitive advantage,” said Dr. Martin Brudermüller, Chairman of the Board of Executive Directors and Chief Technology Officer of BASF, speaking about the circular economy, a key issue of the future in society and in politics. BASF has therefore launched a new Circular Economy Program. By the year 2030, the company aims to double its sales generated with solutions for the circular economy to €17 billion. To achieve this, the company is concentrating on three action areas: circular feedstocks, new material cycles and new business models. As of 2025, BASF aims to process 250,000 metric tons of recycled and waste-based raw materials annually, replacing fossil raw materials. “The path to a circular economy will require enormous efforts on our part. But we have taken on this challenge with commitment and creativity and we can build on our innovative strength,” said Brudermüller. The Chairman of the Board of Executive Directors and scientists presented examples from BASF’s research pipeline today at the first digital Research Press Conference.
Battery recycling: Closing the loop in e-mobility
According to experts, more than 1.5 million metric tons of battery cells from electric vehicles will have to be disposed of in the year 2030. In addition, there is scrap from the production of cells and cathode active materials as well as their precursors. These contain valuable resources such as lithium, cobalt and nickel. With battery recycling, these raw materials can be reclaimed and reprocessed. To recycle lithium-ion batteries, they are first dismantled and shredded, which creates a substance called “black mass.” It is currently possible to recover raw materials from black mass using various chemical processes. This reduces the carbon footprint of the battery metals by at least 25 percent compared to mining from natural deposits.
Until now, however, this process has been very energy-intensive or has created large volumes of salts that require disposal. In addition, the yield of raw materials is still too low. BASF is developing a new highly efficient chemical process with numerous advantages: It can recover high-purity lithium from the batteries with high yields, it prevents waste and it further reduces the carbon footprint compared to existing processes.
In this way, BASF supports the European Commission’s goals of establishing a sustainable European battery value chain. The BASF recycling process can play an important role in the creation of a circular economy for batteries in Europe.
Additives to improve plastics recycling
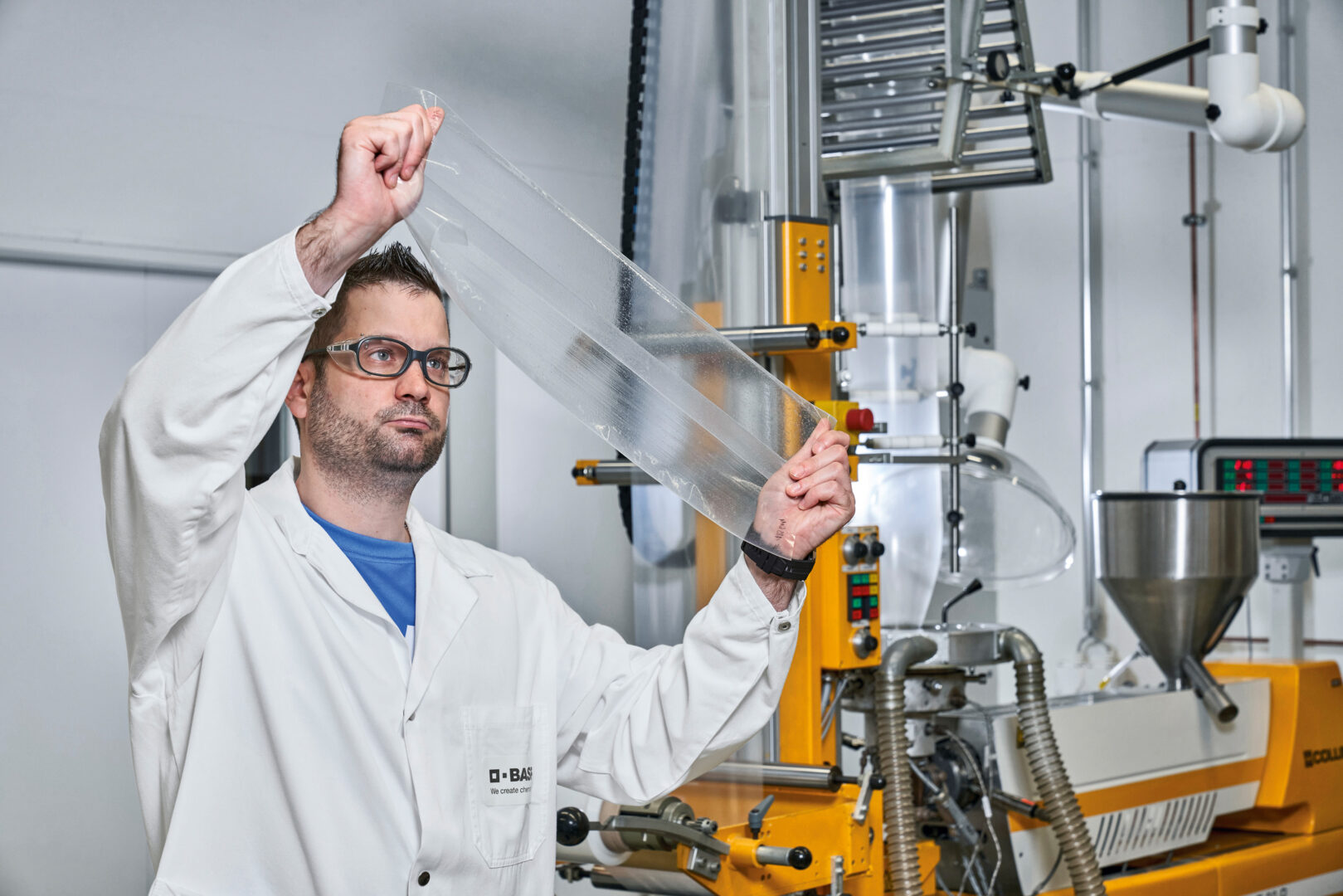
Due to the repeated use and processing of the plastics the polymer chains will be damaged so much that the plastic becomes brittle or yellowed. Additionally, the plastic waste is often made up of a mixture of different plastic types which cannot be separated from each other. Such mixtures of incompatible plastics have a significantly negative impact on quality.At BASF’s research scientists are working on developing additives that can specifically stabilize recycled plastics and improve their properties. This enables plastics to be mechanically recycled multiple times and and material loops can be closed more effectively and more often.Daniel Santoro, lab technician at the Application Center for Plastic Additives in Kaisten (Switzerland), compares the optical properties of a recyceld film with and without a stabilizer package. Photo: BASF
For plastics as well, BASF researchers are working on ways to more efficiently close material loops. According to a study by the consulting firm Conversio, around 250 million metric tons of plastic waste are globally generated per year. Only around 20 percent of this plastic is recycled, thus keeping the material in circulation. In mechanical recycling, waste plastics are shredded and melted to make recyclate, which is then used to make new products. However, this material is not suitable for many applications without further processing. One reason is that repeated use and processing often damage the polymer chains so much that the plastic becomes brittle or yellowed. Another reason is that plastic waste is often made up of a mixture of different plastic types which cannot be separated from each other. For example, beverage bottles are made of polyethylene terephthalate (PET), while their lids are usually made of polypropylene (PP). Such mixtures of incompatible plastics have a significantly negative impact on quality.
BASF researchers have addressed these problems by developing various plastic additive packages to specifically stabilize and improve the quality of recycled materials. Solutions such as compatibilizers will enhance the mechanical properties of polymer mixtures. This upgrades mechanically recycled plastics and the products made from them in a plastics cycle.
Plastic waste becomes a new feedstock for the chemical industry
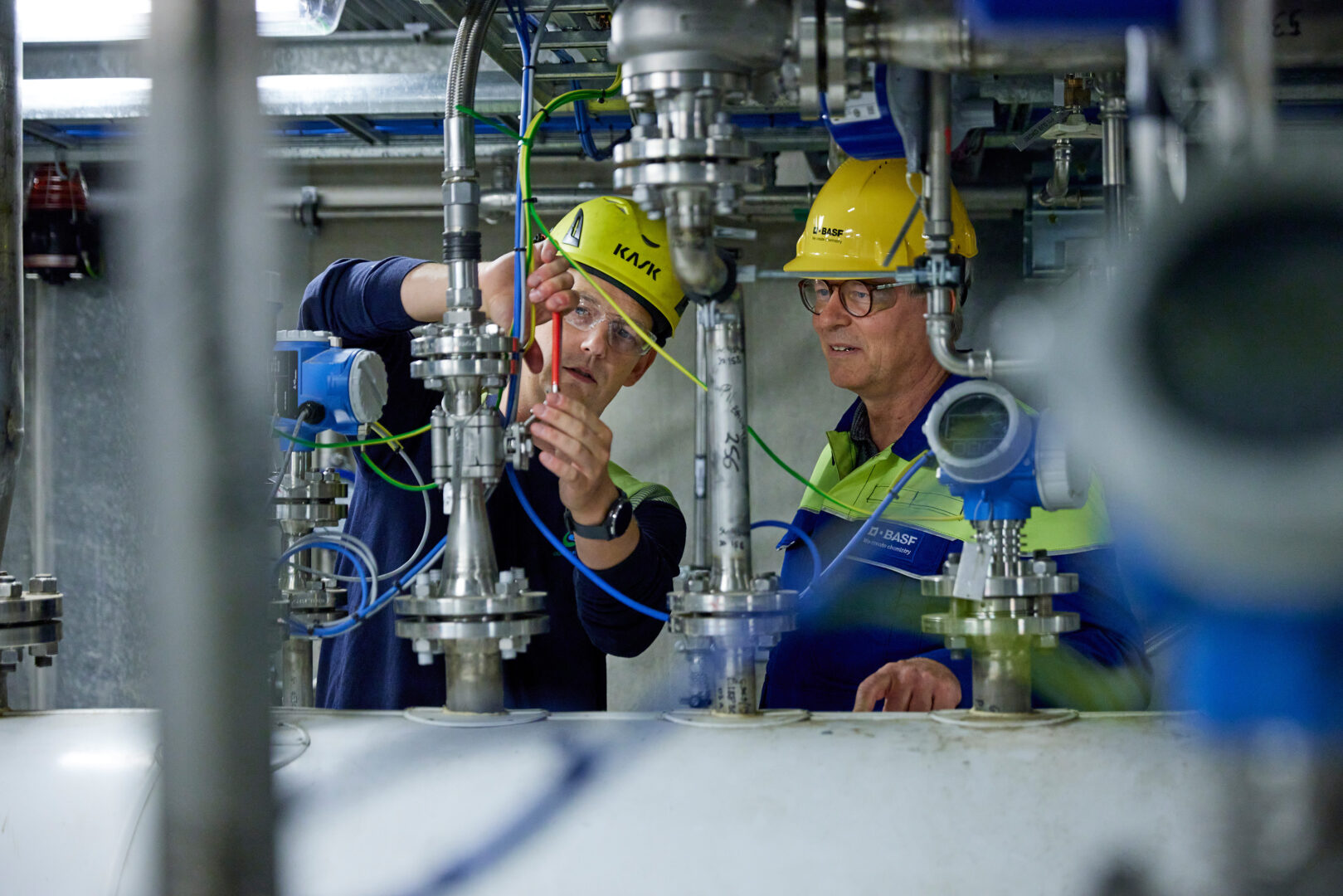
In BASF’s ChemCycling project, plastic waste is transformed into pyrolysis oil using a thermochemical process. The oil can be fed in the BASF Verbund, replacing fossil resources. Using a mass balance approach, new products are manufactured with it. These have the same properties as products from fossil raw materials. BASF works together with partners such as Quantafuel, a start-up headquartered in Oslo, Norway. Quantafuel is specialized in the pyrolysis of mixed plastic waste and the integrated purification of the resulting oil.Rasmus Kærsgaard (left), Plant Director, Quantafuel, and Dr. Michael Bachtler (right), who is working on BASF’s ChemCycling project, in Quantafuel’s pyrolysis and purification plant in Skive, Denmark. Photo: BASF
Each year, 200 million metric tons of plastic waste worldwide go unrecycled. An important complement to mechanical recycling is chemical recycling, which takes a different approach to creating a circular economy for plastics. Chemical recycling transforms plastic waste into secondary raw materials, for example, through a thermochemical process called pyrolysis. The output of this process is pyrolysis oil, which can be used by the chemical industry to make new products. The advantages of this process are that it can also recycle mixed and unclean plastic waste streams. Moreover, products made from pyrolysis oil are indistinguishable from conventional products, so they can be deployed in even the most demanding applications. This means that, for the first time ever, automotive components, medical devices and even food packaging can be made from this kind of plastic waste.
To advance this promising technology, BASF launched its ChemCyclingTM project in 2018. Together with cooperation partners, BASF researchers are working on further developing and improving the process to produce pyrolysis oil from mixed plastic waste. Developing suitable catalysts for the new process technology is an important aspect of this. These catalysts aim to ensure that high-purity pyrolysis oil is always produced, even when the composition of the plastic waste varies. A first-generation catalyst is already integrated in the pyrolysis plant of BASF’s Norwegian partner Quantafuel. To carry out the development work, scientists from the two companies are utilizing the expertise and high-throughput test labs of BASF’s subsidiary hte in Heidelberg, Germany, and the computing capacity of BASF’s supercomputer.
Rambutan program: Organic raw materials, sustainably sourced
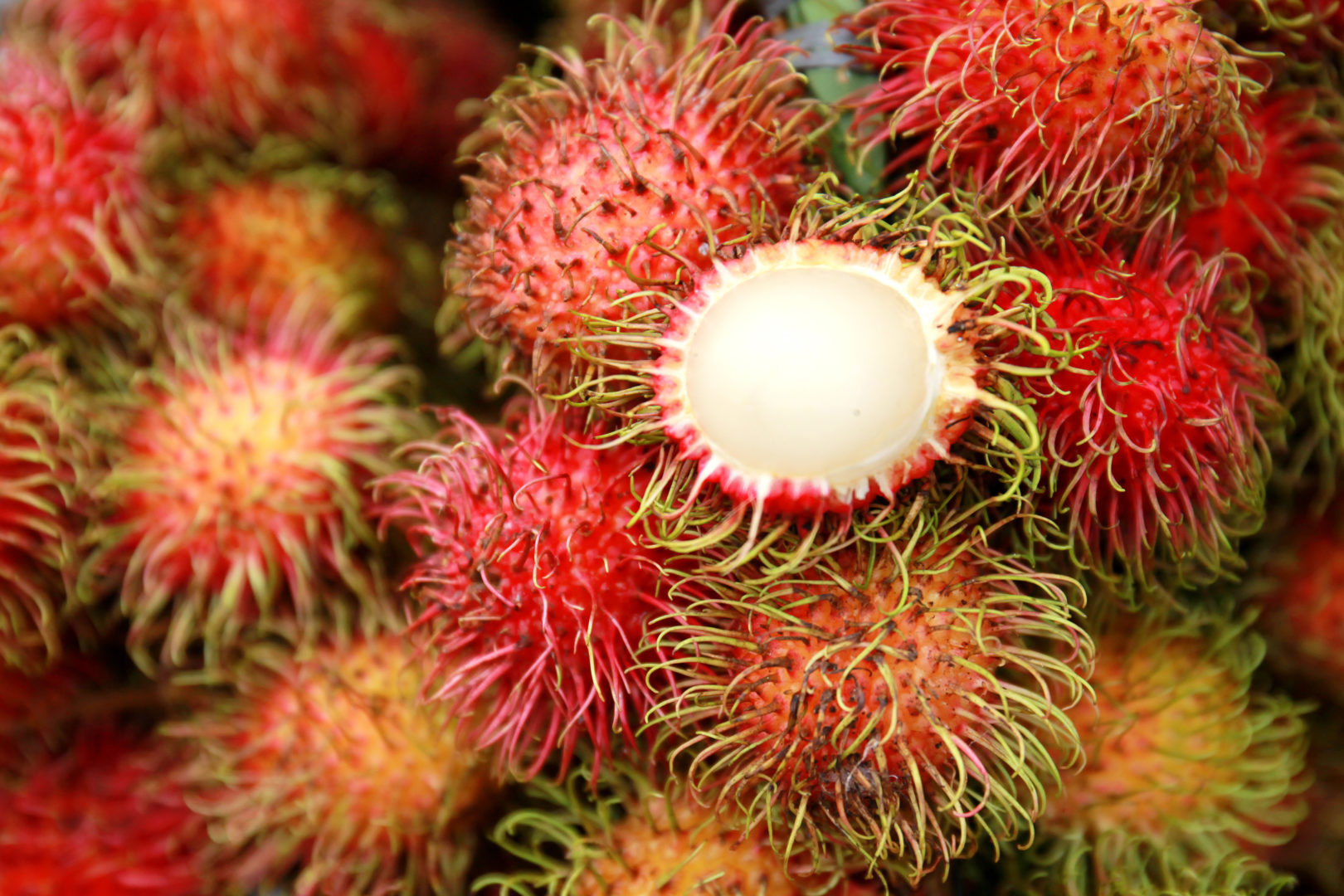
Material loops are also being closed by renewable raw materials. One example is the Rambutan program, which sources high-quality active ingredients from previously unutilized plant parts. BASF researchers discovered that active ingredients from the leaves, peel and seeds of the rambutan fruit have positive effects on skin and hair. In order to sustainably source the cosmetic ingredients, the company’s Rambutan program has established a socially and environmentally responsible supply chain with local partners in Vietnam and initiated the cultivation of the first two organically certified rambutan gardens in Vietnam. Photo: BASF
Renewable raw materials are another pillar of BASF’s Circular Economy Program. BASF plans to further increase the volume of renewable raw materials from sustainable sources in its production. One example is the Rambutan program, which sources high-quality cosmetic active ingredients from parts of a plant that were previously unused. For customers in the cosmetics industry, BASF researchers are always looking for interesting active ingredients in nature, for example, in tree bark, leaves, roots, seeds and fruit. They study thousands of samples every year. This is how they became aware of the substances contained in the rambutan tree (Nephelium lappaceum) – a close relative of the lychee tree. The BASF researchers discovered that an aqueous extract from the leaves of the tree has an activating effect on various human skin genes and promotes the creation of collagen. In addition, active ingredients from the peel and seeds of the fruit have positive effects as they help to increase moisture in the skin and vitalize hair roots. BASF has therefore found a way to not only use the juicy fruit, but also the peels, leaves and seeds, thus ensuring that no part of the plant goes to waste.
To sustainably source the cosmetic ingredients through its Rambutan program, the company has established a socially and environmentally responsible supply chain with local partners in Vietnam and initiated the cultivation of the first two organically certified rambutan gardens in Vietnam. The program enables the workers to earn an above-average income, offers health insurance and ensures safer working conditions. This means the superfruit not only offers benefits for consumers, but also for workers and the local environment.