“In the past, we often had to live with compromise solutions when purchasing standardised conveyor belts. In many cases, the systems lacked adaptability with regard to customer conditions and needs, such as a small footprint. In addition, we were dependent on the supplier with regard to delivery dates,” says Managing Director Manfred Hödl.
These were the reasons that led Redwave to develop conveyor belts specifically designed for the recycling industry. “We know the recycling industry and how different materials behave on convey- ors in the course of several years. The choice of scrapers, belts, etc. is already made during the planning and design process,” continues Manfred Hödl.
This enables an improved and optimised feeding of the materials to the respective machine equipment. Sorting machines, for example, can be optimally fed with conveyor belts that are adapted to the respective recycling materials. This in turn also has a positive effect on the quality of the end product or the throughput.
In addition, compromise solutions, with which customers were confronted in some cases due to external purchasing, are largely eliminated. Where space is limited, no “emergency solutions” are created, but instead individual and efficient customer solutions.
Demands towards the recycling industry
The requirements for conveyor belts in the recycling industry differ significantly from the requirements of other industries such as the automotive, food or mining industries. Even within the recycling industry, the requirements are not identical, because waste glass fragments behave differently from, for example, wastepaper, plastics or scrap metal.
The Redwave conveyor belts have been specially developed for the recycling industry. This concerns improvements of the chute connection for feeding onto the sorting machine or also the easy accessibility, which plays a major role during cleaning and maintenance work, because contamination and blockages are not uncommon in a recycling plant. Therefore, during the development process, great importance was attached to ease of maintenance, low maintenance requirements and user-friendliness of the conveyor belts. For example, removable sheet metal cladding and swivelling floor panels make cleaning easier and minimise the amount of maintenance required. External lubrication points also improve accessibility enormously and offer time savings.
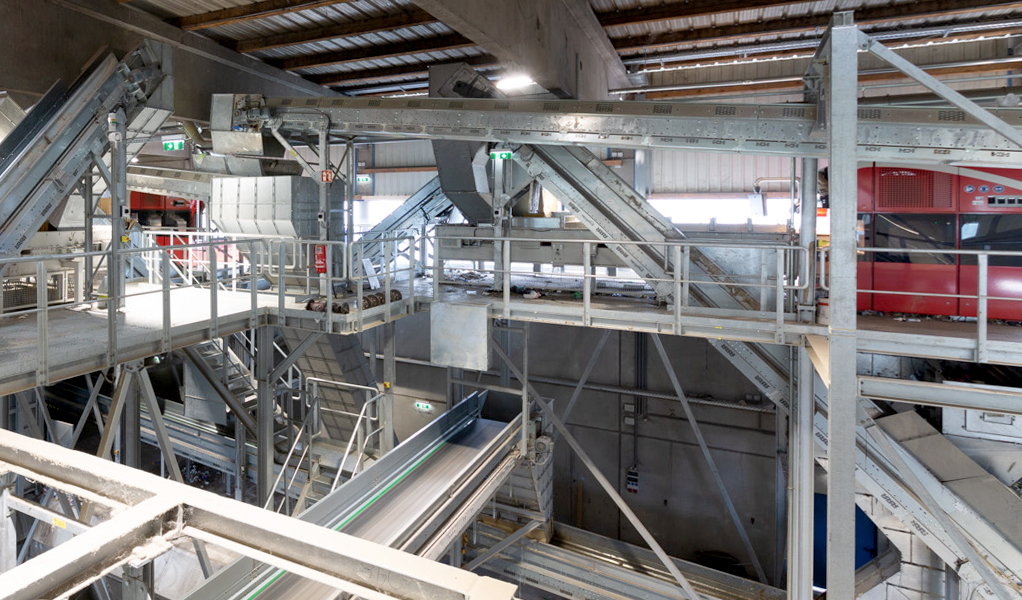
Photo: Redwave
Although the conveyor belts are quick and easy to clean and maintain, they naturally comply with the product-specific applicable European directives and are 100% CE compliant.
Another point in the sorting process that should not be underestimated is the issue of dust formation. For this reason, special solutions have been developed by Redwave for the belt seals (covers and gutter seals), which are adapted to the respective material that is sorted in the recycling plant.
The conveyor belts themselves are currently installed in REDWAVE systems as troughed belt conveyor, sliding belt conveyor and chain belt conveyor.
Flexibility and durability
A highlight of these conveyors is their modular design. This allows a simple modification of the conveyor belt length afterwards, but also additional equipment (sensors, weighing system, scraper) can be retrofitted easily.
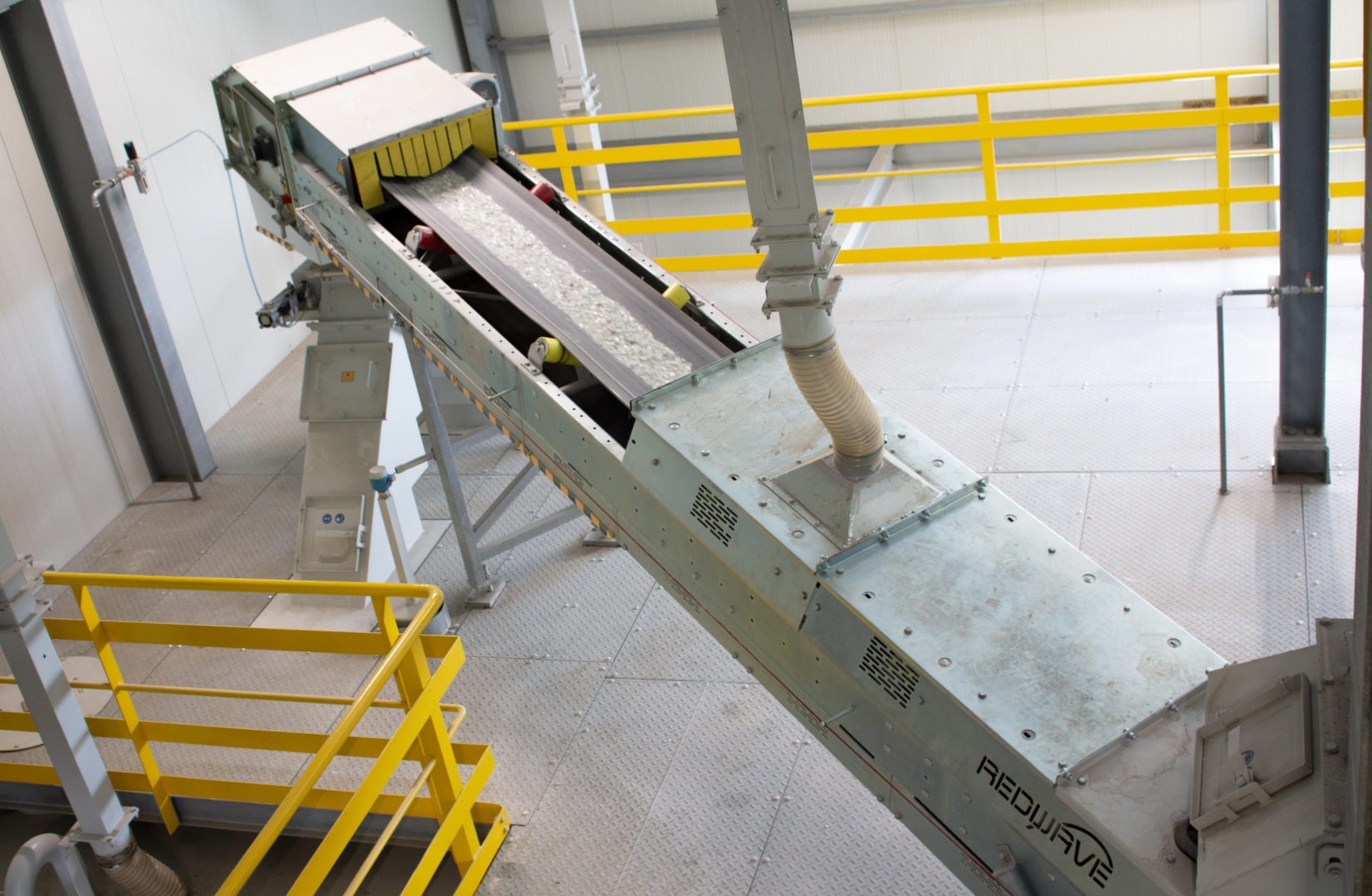
Photo: Redwave
Maximum value is placed on the quality of the purchased parts, which come exclusively from well-known European manufacturers, because only high-quality parts, such as the drive system, the bear- ings, rollers and belts, guarantee a long service life.
A networked integration of the conveyor belts into the entire sorting system should further improve or optimise the sorting process. This integration takes place through the integration of Redwave mate, the intelligent artificial support in the recycling plant.