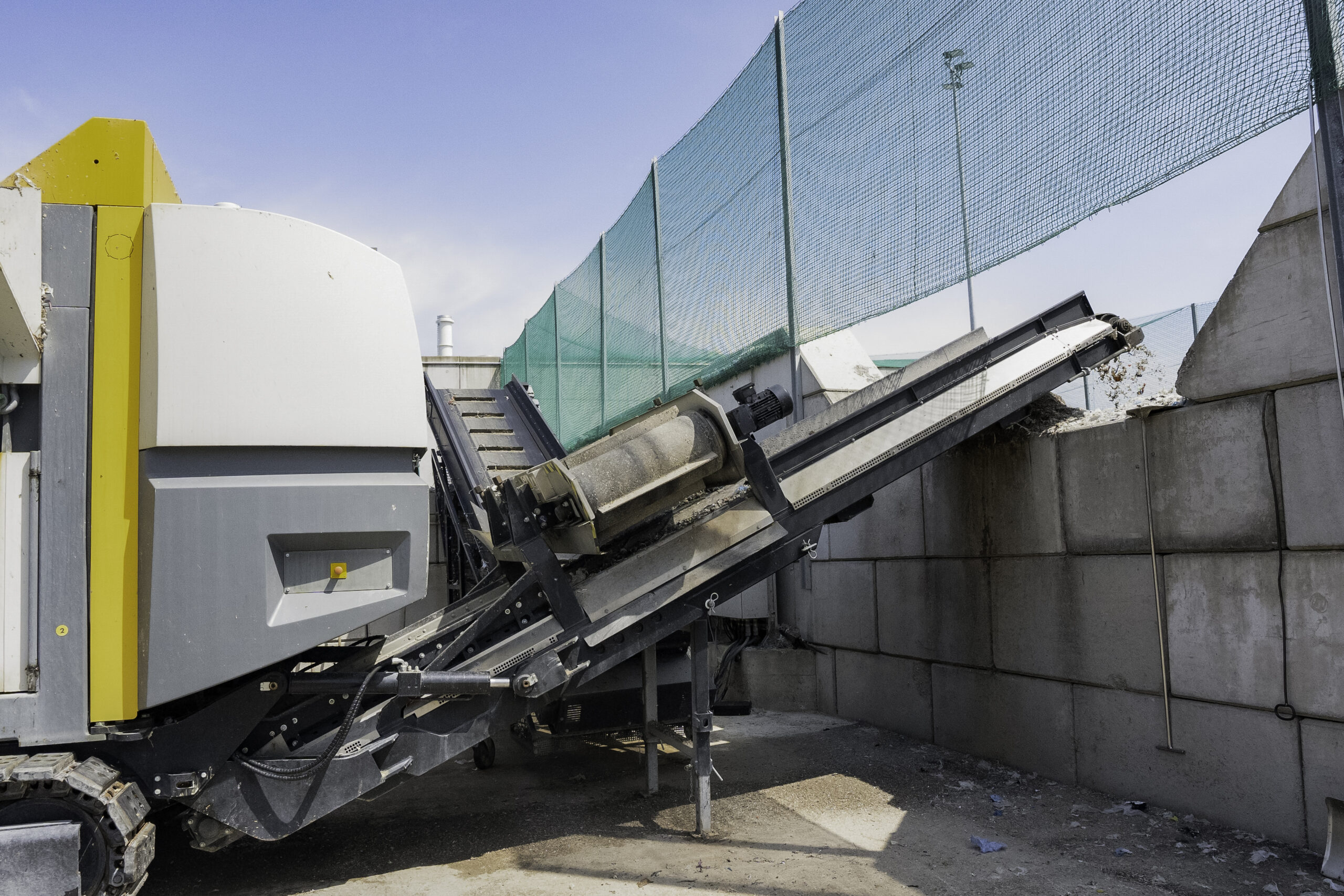
This means that waste accumulated during paper production, for instance pulper ropes (also referred to as pulper waste) and rejects, are re-used and recycled. Shredding pulper ropes is one of the most important process steps for recovering material streams for recycling and for thermal recovery. Laakirchen Papier AG, a member of the international Heinzel Group, has been using an Untha XR3000C mobil-e shredder for its pulper ropes for several years.
“Due to their shape and consistency, pulper ropes are notoriously difficult to process. However, they are well worth the effort as they contain precious materials for recycling, such as metal, as well as other waste materials that may be used as alternative fuels in energy production,” says Daniel Wresnik, Team Leader XR/ZR Sales & Demonstrations DACH Region at Untha.
Pulper ropes: a challenging source of valuable materials
Pulper ropes are a by-product of wastepaper recycling. Their name derives from the term “pulper”, a large vat that is used in paper mills for dissolving paper and pulp. Wastepaper usually also contains impurities such as plastics (foils, stickers), small metal parts (staples and paper clips) as well as textiles (threads from bookbinding) etc. To remove these from the pulp, wire ropes are lowered into the pulper and the contaminants get caught up in them. This is how the so-called “pulper ropes” are produced. At Laakirchen Papier AG, these ropes are four to seven metres long and have a diameter of up to 70 centimetres. When they are removed from the pulper, they are wet, which creates yet another obstacle for their further processing. However, the material contained in the pulper ropes is valuable and can be recycled and reused. Metals, for instance, may be sold and recycled. The other residual materials are used as alternative fuels in energy production. In this way, a challenging waste product may be put to commercial use.
Untha XR class for efficient shredding
To separate the individual materials and prepare them for recycling or alternative fuel production, the pulper ropes must first be shredded. The UNTHA shredders of the XR class rise to the challenge: The models XR2000/3000 (mobile and stationary) are particularly energy-efficient due to the innovative UNTHA Eco Power Drive, shredding pulper ropes to a homogeneous granulate in a single-step process. The slow-running cutting unit makes single-shaft shredders particularly resistant towards non-shreddables as well as low-maintenance. The fully automated pusher system ensures continuous material feed. With the C-cutting system, the XR shreds pulper ropes down to a defined fraction size of 50–150 mm, depending on the perforated screen used. With an overbelt magnet, metal parts are pulled out from the granulate. The separated materials may then be used for recycling (metal) as well as for thermal recovery (plastics, textiles).
The paper industry relies on the Untha XR3000C mobil-e
Laakirchen Papier AG is part of the internationally active Heinzel Group and produces up to 780,000 tonnes of environmentally friendly publication and packaging paper every year, made exclusively from recycled fibres. 98.3 percent of production waste is used for material or thermal recovery. For shredding the 25 tonnes of pulper ropes produced daily, Laakirchen Papier has been using an UNTHA XR3000C mobil-e for several years. “The UNTHA XR fulfils all our expectations. The shredder is energy-efficient and powerful at the same time. The output is extremely well-suited for material and thermal recovery, enabling us to make commercial use of the waste we produce. This helps us to pursue our goals in terms of sustainability and conservation of resources”, says Johann Stadlmayr, project manager at Laakirchen Papier AG.