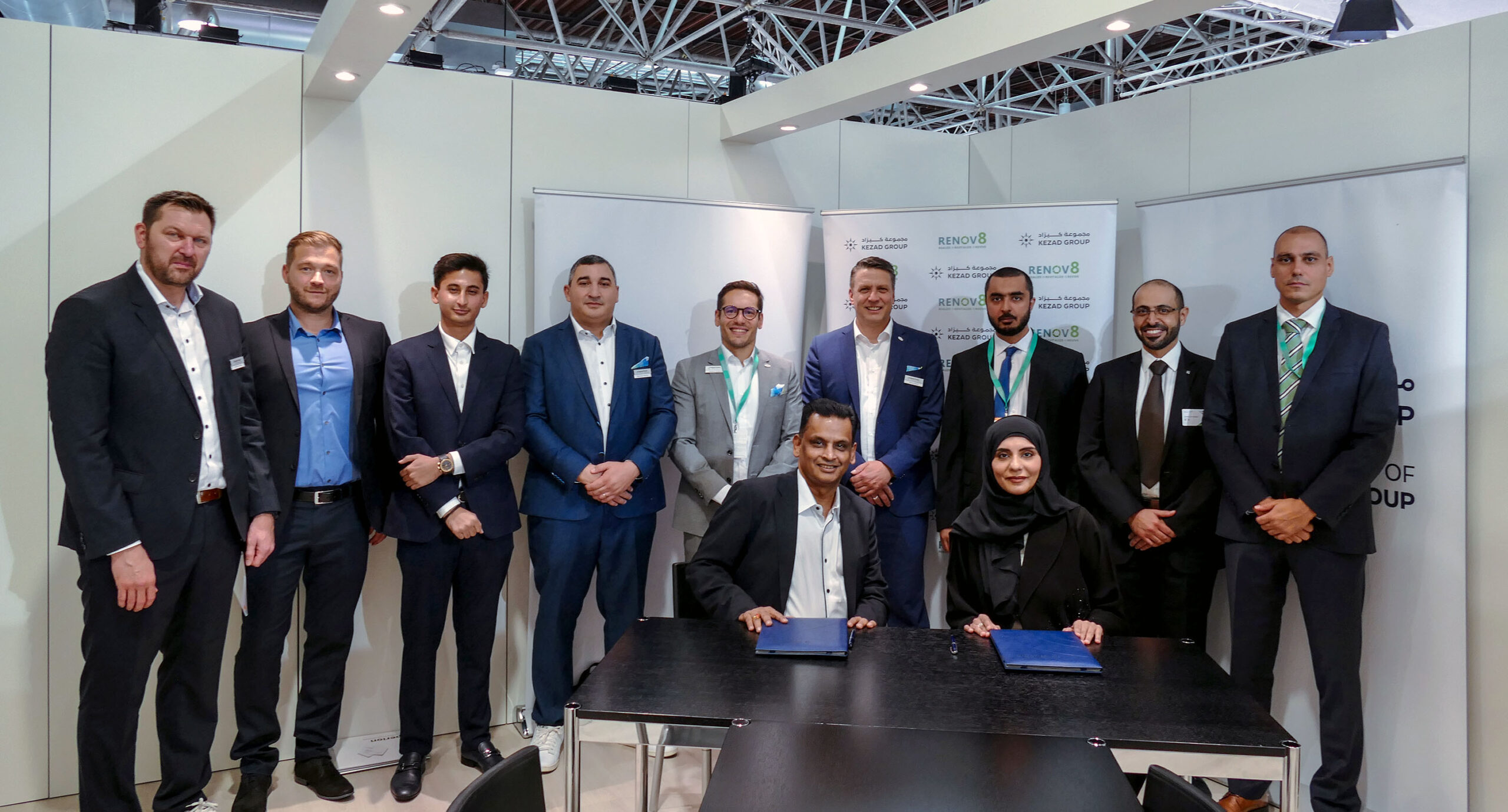
The Coperion system for the chemical recycling of PMMA will be installed at the Kezad Polymers Park in Abu Dhabi, which is among the most popular vertically integrated Polymers downstream manufacturing eco-systems in the region. It will thermally convert PMMA into liquid rMMA in a continuous process. The system includes material handling, two ARW discharge agitators with discharge screws and two Smart Weigh Belt (SWB) feeders, as well as a ZSK 92 Mc18 twin screw extruder with 92 mm screw diameter, a vacuum system and a condenser. Key components of the system are produced in-house by Coperion.
Nilesh Jain, founder of Renov8, visited Coperion at its booth at K 2022 to sign the contract. The conclusion of the contract was preceded by extensive tests on the chemical recycling of PMMA at Coperion’s Test Center.
Coperion’s process solution allows for the thermal recycling of PMMA to rMMA in a very economical, continuous process.
The PMMA recyclate is conveyed via a discharge agitator ARW and a discharge screw to a Smart Weigh Belt (SWB) feeder. This low-headroom gravimetric feeder weighs large quantities of bulk material at high accuracy and feeds it into a ZSK twin screw extruder.
In the ZSK Mc18 twin screw extruder mechanical energy is introduced into the PMMA via the co-rotating twin screws thanks to a torque of 18 Nm/cm³. The temperature of the melt rises energy-efficiently in a short time. The material depolymerizes. Gaseous MMA is produced, which is extracted via the degassing domes of a vacuum system and then converted into liquid rMMA in a condenser. Coperion’s solution for chemical recycling takes place with lower energy consumption than pyrolysis processes without extruders or compared to recycling with single screw extruders.
The chemical recycling system for Renov8 will allow the processing of two separate product streams. Thanks to its self-cleaning properties, PMMA with different light transmittances can be recycled on the same ZSK 92 Mc18 twin screw extruder in short time without loss of quality.