Since using the baler, disposal processes have slimmed down enormously. Mr. Reindl, Supervisor, Ingram Micro Distribution GmbH reports: “Our time savings are tremendously high. “We save seven hours a day, by using the BaleTainer.”
BaleTainer compacts the resulting cardboard out of two storage areas. Centrally positioned, the baler allows filling from the lower and upper storage area. This was also the key to the enormous time savings, reports Reindl. Now the company benefits from short and fast disposal routes.
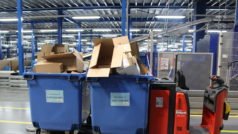
The employees are also happy about the fully automatic baler. They throw the packaging, of for example cameras or cell phones, in storage bins, which are placed directly at source where material accrues. In the lower storage area, an employee drives the full bins to the BaleTainer, where they are tipped into the hopper in just 25 seconds using a lifting- device. From the upper storage area, the boxes fall directly into the BaleTainer via a chute. Waiting times are thus avoided by the simultaneous filling possibility from ground and upper level. The BaleTainer compacts the cardboard with 60kN press force into 450kg bales. In addition to the fully automatic compaction, the wire tying and the bale discharge are fully automatic. The disposal is now much faster, Mr. Reindl confirms: “Before, the manual emptying of a container took two to three minutes, the BaleTainer can do it in 25 seconds.”
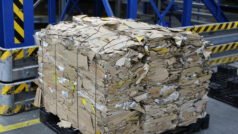
Source: Strautmann
Ingram also saves on transport costs due to the high density of cardboard packaging. The marketing of directly marketable bales is also very lucrative. Mr. Reindl praises: “With the BaleTainer and the uniform disposal containers, we have created order and structure – that was particularly important to us because of the many customer visits.”
„Strautmann offered exactly what we wanted and that too at a fair price. Mr. Günter Komesker, Managing Director Strautmann Umwelttechnik GmbH and Mr. Markus Jobst, Sales Director South-East, gave me good advice and it was fun to design the project with you, “says Reindl. Instead of spending time with disposal, employees can now focus on their core business.
In the past, all outer packaging was collected in containers. These were picked up in the lower storage area by pallet truck and brought to the compactor. The employees had to walk long distances to the compactor, even in case of bad weather conditions, and then manually inserted the cardboard boxes into the compactor- The disposal process of a single container took about two to three minutes. The outside press container also occupied a dock space and occurred monthly rental cost.
In the upper storage area, cardboard was compacted with a vertical baler. Each carton had to be thrown into the press chamber by hand. Through constant intermediate pressing, employees lost a lot of time by disposal. “That was a huge amount of time, a pointless waste of time,” recalls Reindl.